.jpg)
services
Polishing
Kodiak 10-45 Flat Polishing & Mitering Machine
Our Glass Polishing and Mitering Machine features a variable angle of up to 45°, making it the optimal solution for polishing and mitering large, flat surfaces at competitive production speeds. Heavy-duty spindles and frame construction are designed for continuous operation. Polishing the glass edges is the third and final step in glass edge processing. This creates a light and fine shine, which is used above all for furniture and interior design pieces such as glass tables, frameless glass sheets, mirrors as well as sliding glass walls, display cabinets and display windows.
Purpose: Glass polishing serves to eliminate defects that have formed on the surface, such as scratches, scratches or pitting, and restore its original transparency and brightness.
Glass polishing is the removal of scratch and mineral damage from glass surfaces using a polishing machine and a series of abrasive pads and polishing actions.Using glass polishing systems, a skilled glass polisher can remove almost any form of scratch, mineral or spatter damage from any glass surface.
Benefits:Mechanical polishing offers numerous benefits, providing products with an improved surface finish, reduced product adhesion, better surface cleanability, and higher aesthetic appeal.
Glass polishing is the removal of scratch and mineral damage from glass surfaces using a polishing machine and a series of abrasive pads and polishing actions.Using glass polishing systems, a skilled glass polisher can remove almost any form of scratch, mineral or spatter damage from any glass surface.
Benefits:Mechanical polishing offers numerous benefits, providing products with an improved surface finish, reduced product adhesion, better surface cleanability, and higher aesthetic appeal.
Polishing Application
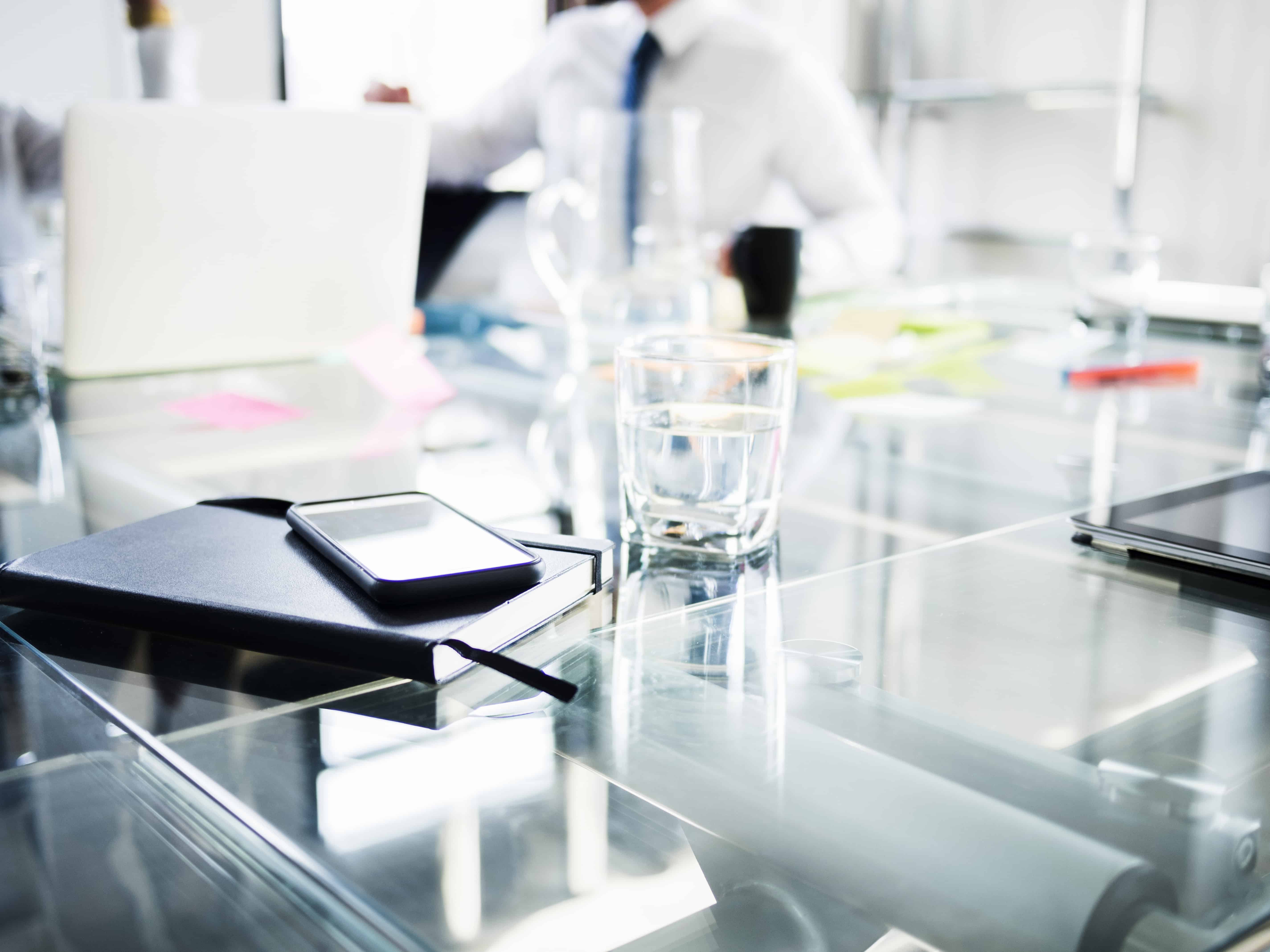
Table Tops
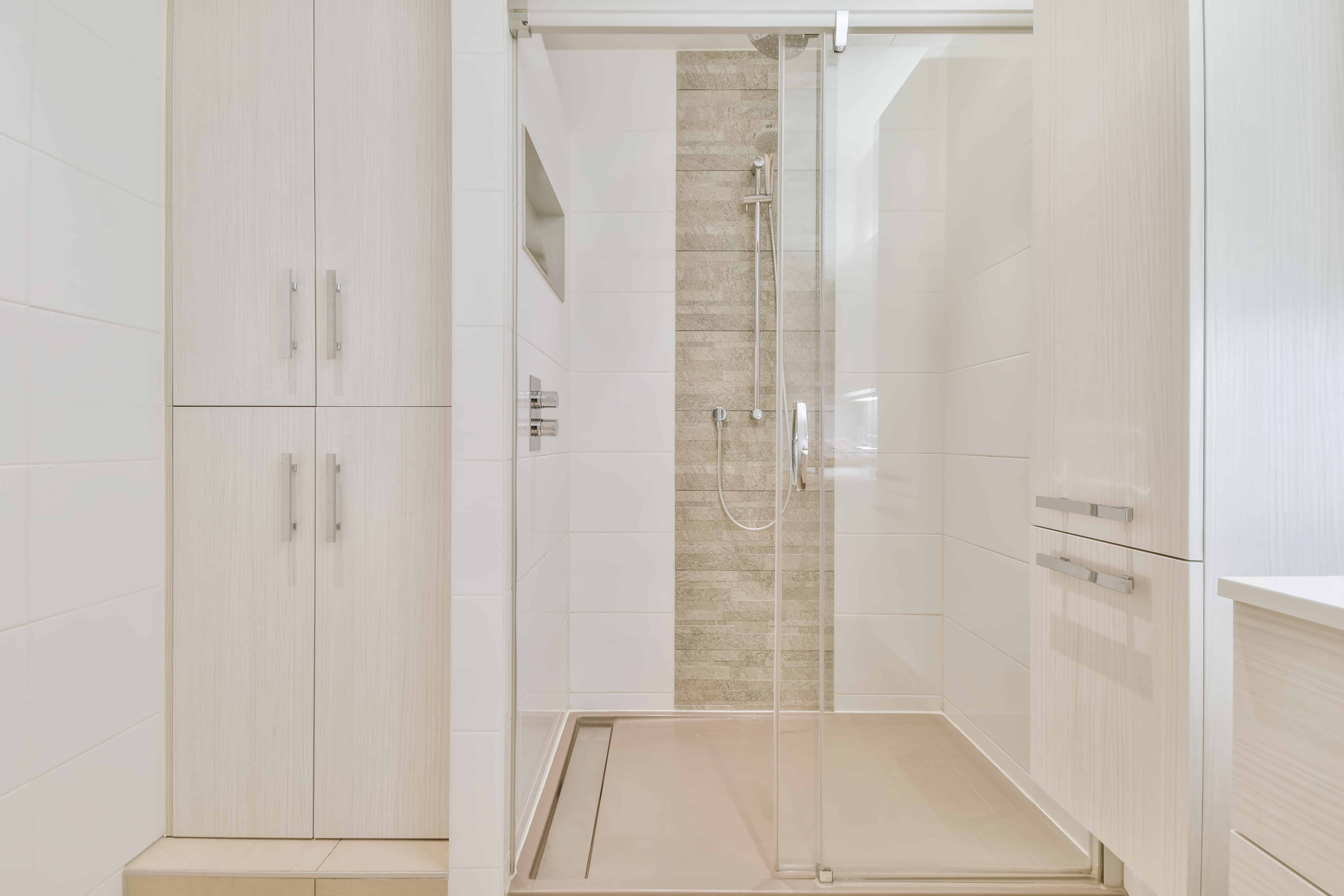
Shower Glass
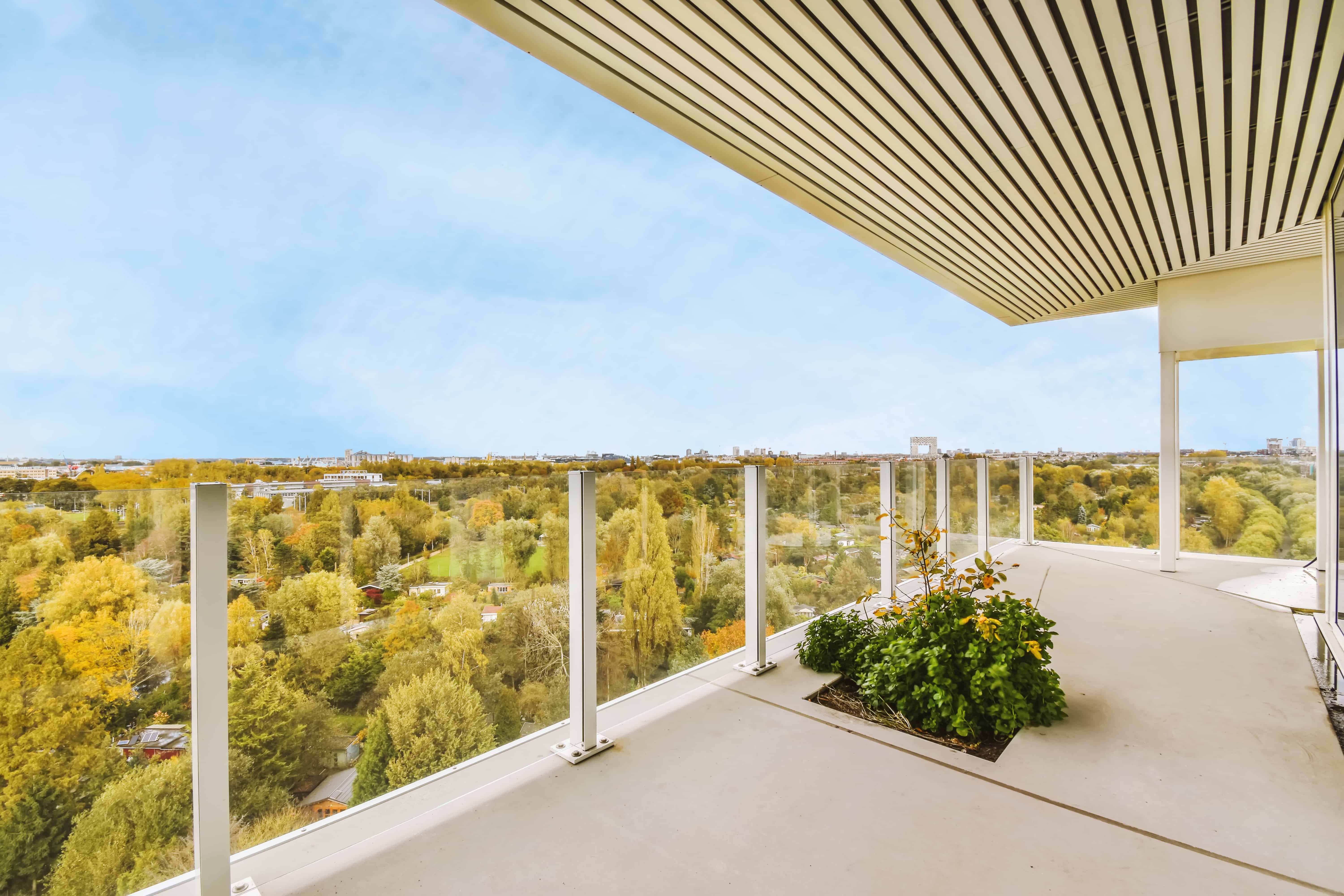