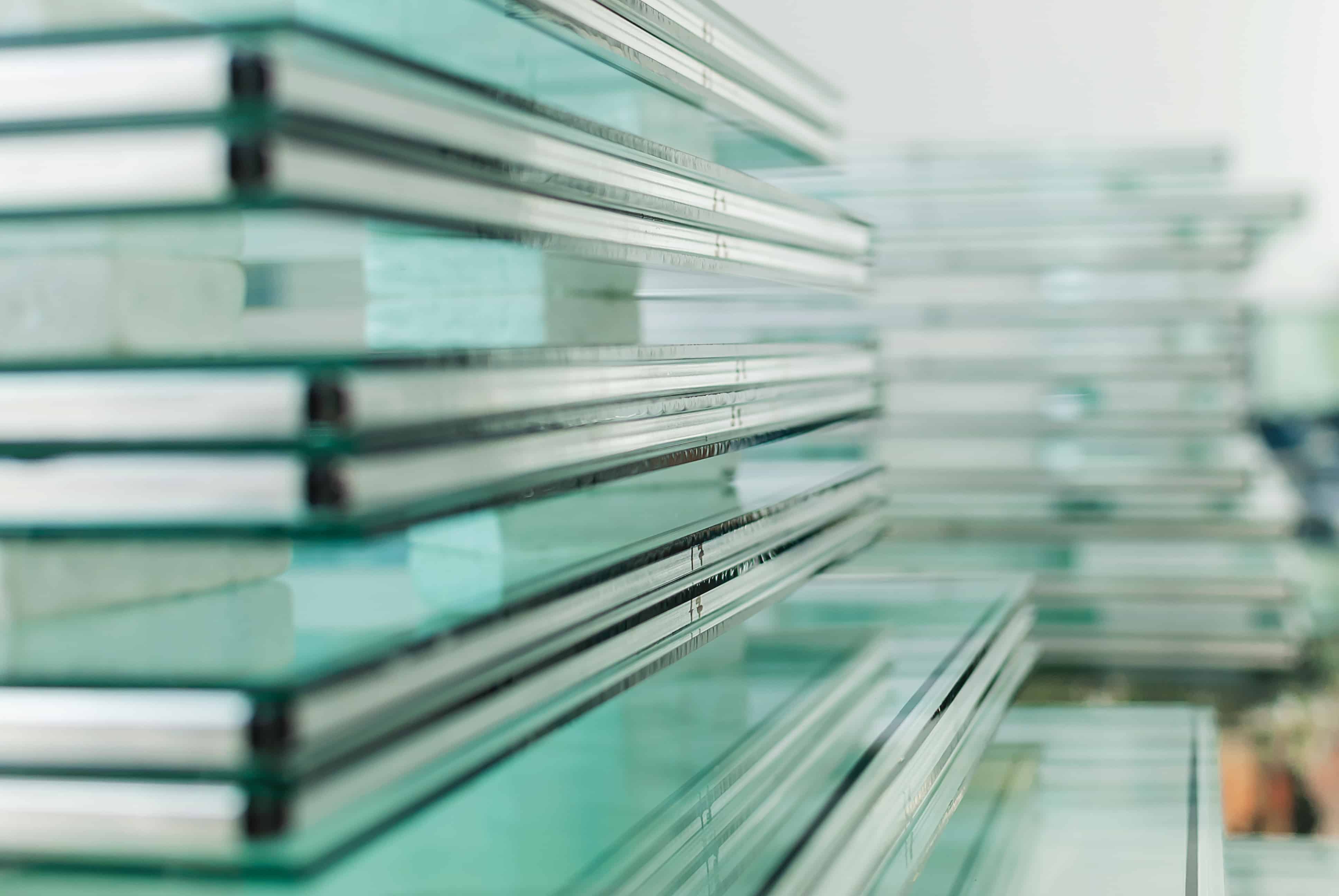
services
IG Units
IG Units are two panes of glass that have been sealed together to create a thermal barrier. The gap between the two panes is filled with argon, and the unit is sealed tightly for maximum insulation. This helps keep heat in during cold weather and out during hot weather, reducing energy bills. IG Units are often used in both residential and commercial applications, due to their energy efficiency.
The most common types of IG units are double pane windows, triple pane windows, and Low-emissivity (Low-E) coated glass. Double pane windows use two layers of glass with an argon gas-filled space between them, while triple pane windows use three layers of glass with two argon gas-filled spaces between them. Low-E coated glass is specially designed to reflect heat, making it even more energy efficient.
IG Units are durable and feature long lifespans, so they make great investments for any home or business. Additionally, the units come in a variety of shapes and sizes to fit any window size or style. Furthermore, they are easy to install and require very little maintenance. With all of these benefits, it’s easy to see why so many people choose IG Units for their buildings.
Our IG Units products are produced locally, end to end.
IG Units are durable and feature long lifespans, so they make great investments for any home or business. Additionally, the units come in a variety of shapes and sizes to fit any window size or style. Furthermore, they are easy to install and require very little maintenance. With all of these benefits, it’s easy to see why so many people choose IG Units for their buildings.
Our IG Units products are produced locally, end to end.
IG Units Application
Residential glass
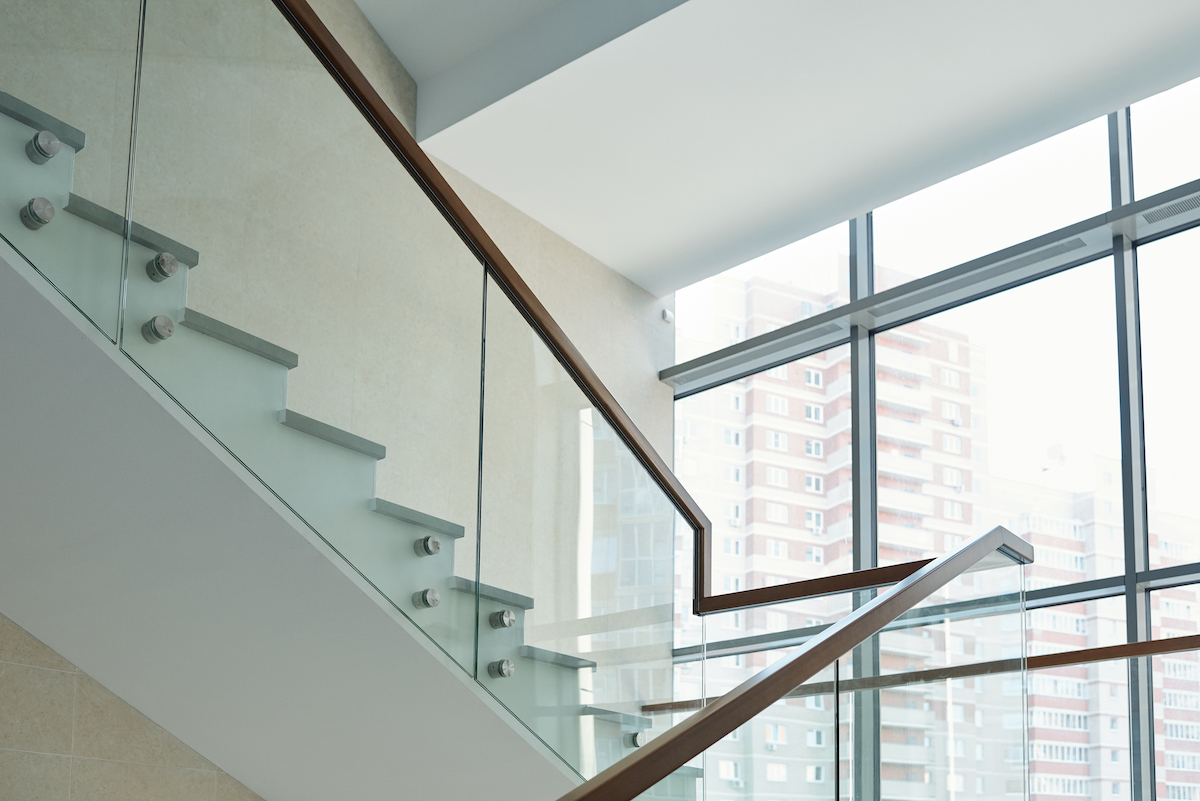
Curtain Wall
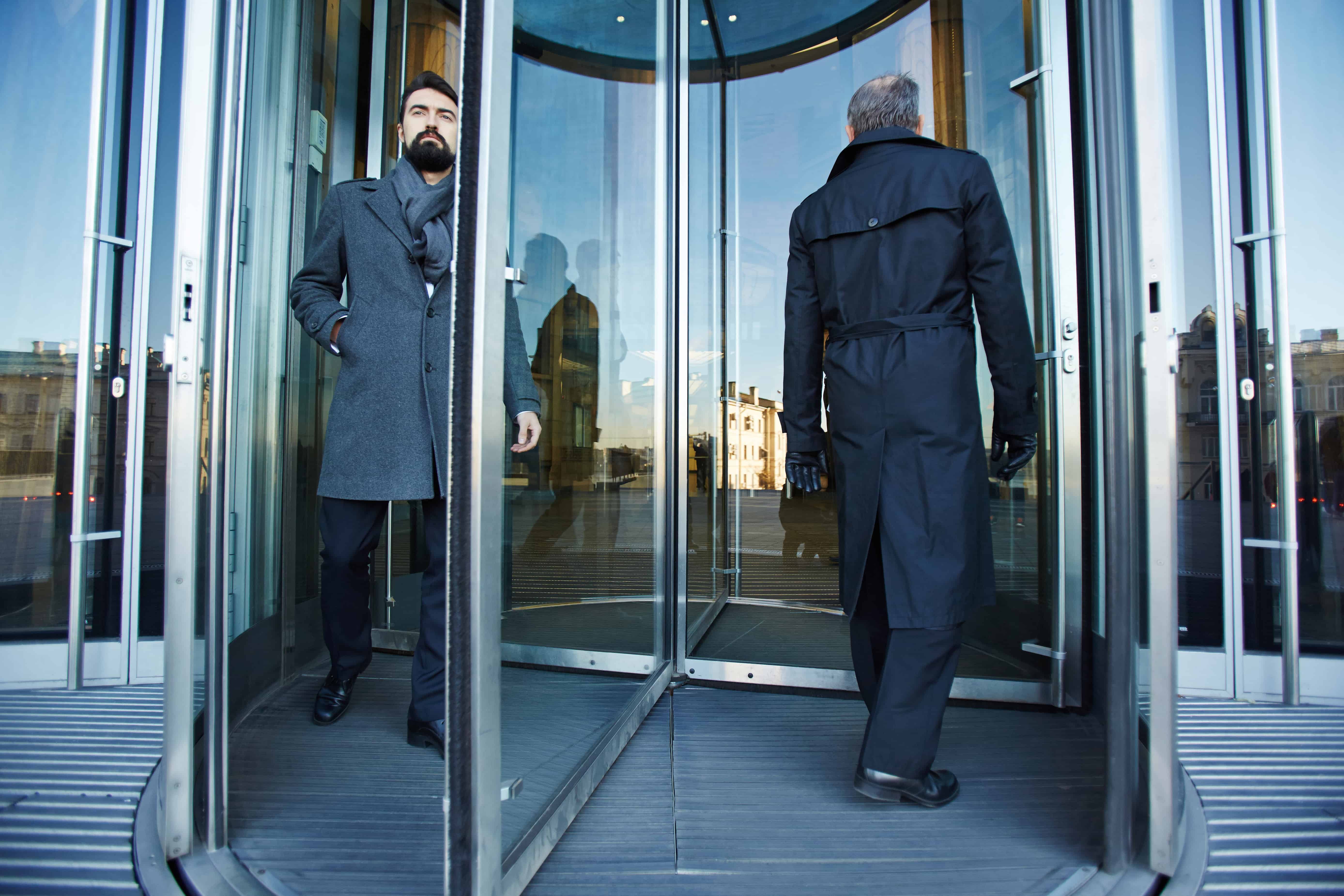